Лазерная резка металла: Первый опыт
Совсем недавно стала широко доступна крутая технология – CNC лазерная резка по металлу.
Я давно хотел её опробовать, и наконец – это свершилось!
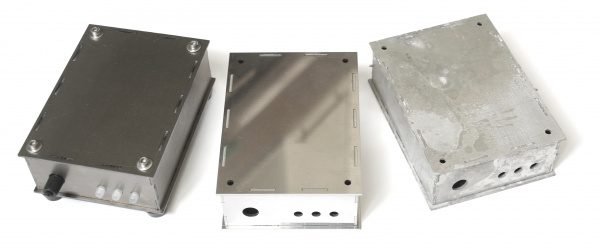
В статье мы рассмотрим процесс создании чертежа, как происходит процесс заказа, ну и что же получилось из 3-х опробованных металлов: углеродистой стали, нержавеющей стали, и алюминия.
Скажу заранее – была допущена туча косяков, и заказать тоже было не просто. Поехали! :)
В целом, связались мы с лаз. резкой металла т.к. появилась необходимость создать кастомный экранирующий корпус для проекта TeslaBoogie, он же гитарный прерыватель для трансформаторов Теслы.
Но проект этот пока на столь ранней стадии, что просто не ясно какой корпус ему делать, ну и дабы просто освоить лазерный металл – пробный экземпляр был нарисован под SimpleDriver.
Чёртёж я рисовал в SolidWorks, в том же стиле как и корпуса для лазерного дерева.
Там же очень полезно собрать отдельные детальки в корпус и проверить нет ли каких-то ошибок:
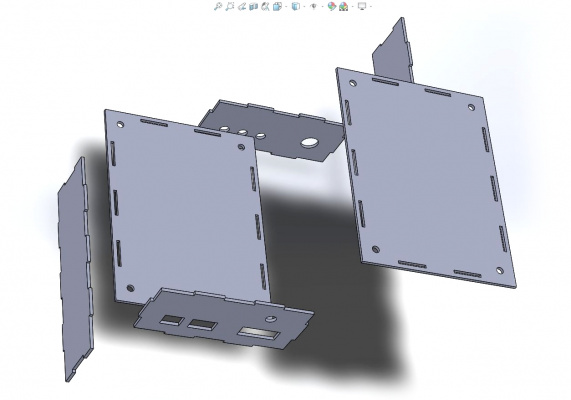
Как только всё проверено – детальки экспортируются в формате .DXF, в идеале ещё добавить скриншоты того как изделие выглядит в готовом виде… И можно отправлять изготовителю!
Скажу наперёд, здесь уже была допущена первая ошибка. :)
В привычной мне резке дерева и акрила лазерный луч просто идёт по сверхтонкой линии на чертеже, оставляя примерно 0.2 мм зазор – т.е. любую конструкцию можно рисовать 1:1, и та легко соберётся благодаря уже заложенному зазору в 0.1 мм.
Но при лаз. резке металла правила другие, и больше соответствуют миру фрезеровки.
Луч по металлу снимает уже около 0.7 мм, и ЧПУ нужно программировать дабы тот резал краешком луча, а не просто шел по линии. Здесь же возникает серьёзная проблема радиусов внутреннего угла, когда вырезать идеально квадратное отверстие становится невозможным.
В итоге, если конструкция как у нас опирается на перпендикулярное удержание деталей в пазах – в чертеже нужно закладывать что любой внутренний угол будет с радиусом 0.6 мм.
На самом деле, все эти нюансы я пытался выпытать у контор-резчиков, но в 100% случаев они на подобные вопросы не отвечают из-за загруженности – о чём вкратце в следующем параграфе.
Всё вышеперечисленное может показаться ужасным примером, как люди могут не уметь, или не хотеть работать – но как показывает практика, именно так оперируют конторы у которых никогда не бывает дефицита с заказами.
И прибыв на место мы в этом убедились.
Это фотка Google Street View от 2015-го года где пока всё пусто, но в 2019-м там весь двор заложен материалом, кубами готовых заказов, и вокруг бегают люди примерно как по муравейнику. :)
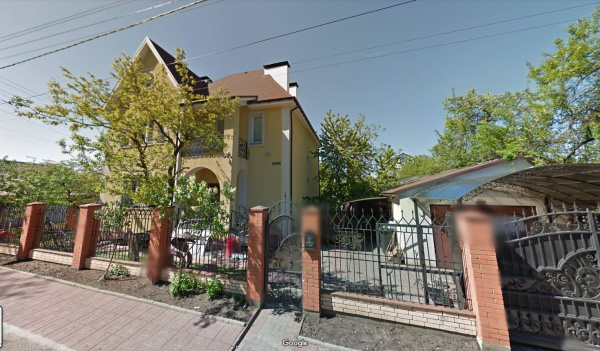
Внутри дом оказался полностью переоборудован под офисы, складские помещения и т.п. – как минимум там постоянно работают человек 20. На втором этаже нам быстро отдали пакет с деталями, и готово.
Но мы ещё задержались, т.к. там было несколько интересных стендов с готовыми образцами.
Там же, из кабинета колл-центра мы краем уха услышали очень крутую цифру – оказалось что ихний лазерный станок загружен примерно на 1000 часов вперёд, или же 41 день.
Вот примерно так обстоят дела, так что получить наши 3 коробочки в течении 2-х недель это ещё было быстро. :)
Кстати, судя по тому что мы видели во дворе – типичными заказами для этой конторы являются 50-200 комплектов за раз, причем не просто вырезанные, а и с элементами CNC-гибки.
Кстати, уже на месте стало ясно, что коробочки по моему чертежу не собираются. :)
Дядька, отдававший детальки сразу пояснил что нужно было учесть радиусы – в принципе справедливо, так что уже дома мне пришлось поработать надфилем дабы чуть сточить крепёжные зубцы стеночек.
Ну, а когда коробки уже собраны – давайте посмотрим что получилось!
В общем, действительно красиво:
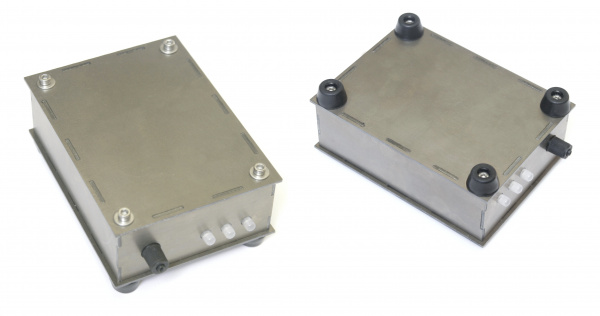
Этот корпус я собрал первым, и в него же пошла платка SD для теста.
Прямо, будто для неё и сделано(гы-гы), жаль что у SD уже есть свой замечательный корпус. :)
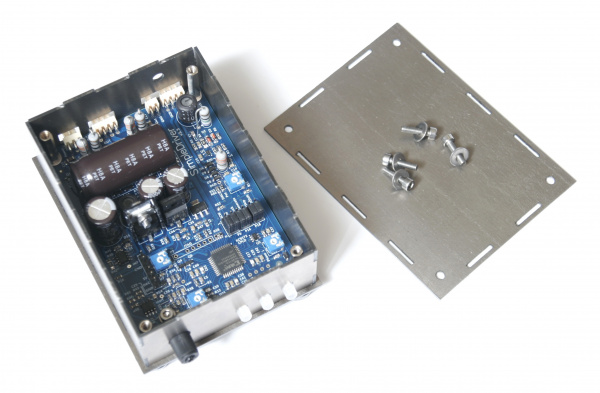
Но красота красотой, всё же не стоит забывать с чем мы имеем дело. Даже при наличии специального оксида, не хранись эта коробочка в музейных условиях – она всего за несколько лет окрасится в коричневый. :)
Даже забирая детальки – они уже были смочены в масле дабы дополнительно предохранить их от коррозии.
По-правильному, для долговечности простую сталь обязательно в начале отдают на пескоструйную обработку, а после покрывают слоем порошка или краски. Для особой долговечности – ещё и слоем лака.
Наиболее распространен такой подход в автомобилях, где кузова традиционно делают из обычной стали для удешевления производства, а потом красят и лакируют – иначе те бы покрывались ржавчиной менее чем за год.
В контраст этому, будь корпус любого авто сделан из нержавейки – он совершенно не нуждался бы в покраске, оставаясь несгниваемым на протяжении многих десятилетий вперёд. :)
Если конечно у вас не идут кислотные дожди, но так ведь – и золото растворяется в царской водке.
Кромка получилась немного острая, и всё время казалось что об детали из нержавейки можно порезаться – благо этого не случилось. Обращаясь с этими детальками есть чувство как будто это осколки кухонного ножа – очень твёрдые, прочные, и звенят как монеты.
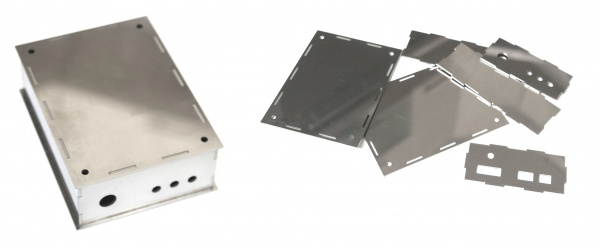
Выглядит корпус по-своему привлекательно, как будто сделан из зеркала т.к. использовался шлифованный лист.
Плюсы у этого материала достаточно значительные – нержавейка очень инертный материал, устройство в таком корпусе буквально можно закопать в землю на 100+ лет, и достать его абсолютно таким же блестящим.
Прочности так же не отбавляй, такой корпус можно бросать об стену, по нему можно проехаться КАМАЗом и тот наверняка выдержит.
Что есть хорошо!
Но что же касательно недостатков?
Я почти сразу заметил что нержавейка царапает сама себя – причем абсолютное большинство царапин возникает ещё при хранении т.к. листы трутся друг об друга. Царапины не особо бросаются в глаза, но на будущее всё же есть смысл найти матовые листы.
Ну и ещё заметка – сплавы нерж. стали бывают очень разные, отличающиеся как по твёрдости, так и по магнитным свойствам. Коробочка, которую вырезали мне оказалась из магнитной стали, что не лучший вариант для работы в мощных электромагнитных полях. Для наших применений нужно обязательно обращать внимание на марку сплава.
Я точно знаю что не магнитится марка AISI 304(она же 08Х18Н10) – но подобных существуют десятки.
Нюансы есть, но в целом – по мне корпуса из нержавейки это пока самый привлекательный вариант, в частности т.к. они не потребуют последующей обработки и могут собираться из деталек «как есть». Нержавейка так же позволит нанести на неё практически вечную гравировку лазером, в отличии от нанесения надписей краской, или вообще наклейками которые слезут уже в первый год.
Local P.S. У меня есть некая тяга к вечным вещам. :)
Конечно, можно предположить что детали просто вырезали из гнилого листа с затонувшей подлодки, но судя по тому что торцы тоже имеют оксидацию – поверхность деталей наверняка была покоцана именно в процессе реза.
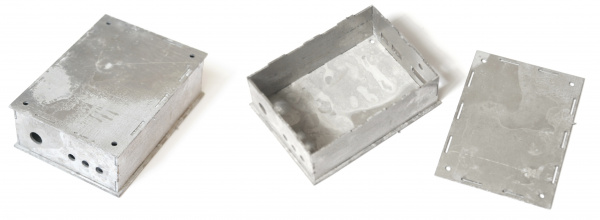
Ну, начнём с того, что опробованная контора оказалось в принципе не режет алюминий лазером – для этого нужны специально заточенные станки, решающие проблему высокой отражаемости IR-диапазона алюминием обратно в оптику, что может разрушить лазер. Даже по мощности, прорезать 1.5 мм алюминий это примерно как резать 10 мм углеродистую сталь. :)
Уже забирая детальки нам сказали что вместо лазера эта коробочка была вырезана другой технологией – «гидроабразивной резкой», более известной как waterjet cutting.
Процесс вообще тоже прикольный, в нём используется струя воды под высоким давлением, в которую подмешаны микроскопические гранулы абразива: en.wikipedia.org/wiki/Water_jet_cutter
Им можно резать такие экзотические материалы как стекло, камень, твёрдую резину, ну и алюминий вплоть до 4+ см толщиной.
Опробовать конечно было интересно, но всё же результат по мне вышел не очень – абразив сильно исцарапал поверхность, и качественно отшлифовать детали такой коробочки займёт часа 2 используя орбитальную шлифмашинку.
Для хоть сколько-нибудь серийного производства это не годится.
В добавок, на каждой алюминиевой детальке есть по вот такому, чуток закрученному усику:
Резка waterjet'ом проходит над ёмкостью с водой, и очевидно – товарищу за станком было влом мочить руку по локоть дабы доставать детали – он выставил галку «не дорезать», а потом открутил детальки с алюминиевого листа.
Если здесь так – думаю с оксидацией тоже как-то нарушили технологию – например деталь лежала мокрой, и у неё не мог образоваться защитный оксидный слой. Так то, в сети полно фотографий ватерджет-резки где на выходе абсолютно чистые алюминиевые детальки.
В общем, с алюминием ещё буду пробовать – причем желательно найти именно лазерную резку, ибо струя ватерджета достаточно не малая – судя по радиусам на внутренних углах она уже достигает где-то между 1 и 1.5 мм.
О нюансах мы уже знаем, так что следующими на очереди будут рабочие корпуса для гитар-интерчика. :)
При следующем заказе я обязательно поинтересуюсь что же случилось с алюминием, резать буду из матовой немагнитной нержавейки с учётом внутренних углов, ну и чисто ради теста надо ещё опробовать гибочку, может когда пригодится.
Как обычно, если у вас есть вопросы или замечания – их можно оставить в комментариях снизу, или же написать мне на почту: eugene.negrobov@gmail.com
Кто дочитал простыню – молодец. :)
Я давно хотел её опробовать, и наконец – это свершилось!
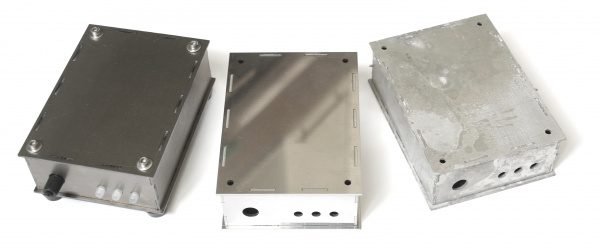
В статье мы рассмотрим процесс создании чертежа, как происходит процесс заказа, ну и что же получилось из 3-х опробованных металлов: углеродистой стали, нержавеющей стали, и алюминия.
Скажу заранее – была допущена туча косяков, и заказать тоже было не просто. Поехали! :)
Создание чертежа
Перед тем как что-то заказать – его естественно нужно нарисовать. :)В целом, связались мы с лаз. резкой металла т.к. появилась необходимость создать кастомный экранирующий корпус для проекта TeslaBoogie, он же гитарный прерыватель для трансформаторов Теслы.
Но проект этот пока на столь ранней стадии, что просто не ясно какой корпус ему делать, ну и дабы просто освоить лазерный металл – пробный экземпляр был нарисован под SimpleDriver.
Чёртёж я рисовал в SolidWorks, в том же стиле как и корпуса для лазерного дерева.
Там же очень полезно собрать отдельные детальки в корпус и проверить нет ли каких-то ошибок:
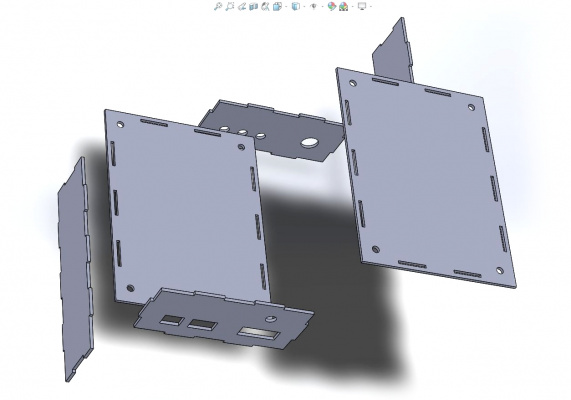
Как только всё проверено – детальки экспортируются в формате .DXF, в идеале ещё добавить скриншоты того как изделие выглядит в готовом виде… И можно отправлять изготовителю!
Скажу наперёд, здесь уже была допущена первая ошибка. :)
В привычной мне резке дерева и акрила лазерный луч просто идёт по сверхтонкой линии на чертеже, оставляя примерно 0.2 мм зазор – т.е. любую конструкцию можно рисовать 1:1, и та легко соберётся благодаря уже заложенному зазору в 0.1 мм.
Но при лаз. резке металла правила другие, и больше соответствуют миру фрезеровки.
Луч по металлу снимает уже около 0.7 мм, и ЧПУ нужно программировать дабы тот резал краешком луча, а не просто шел по линии. Здесь же возникает серьёзная проблема радиусов внутреннего угла, когда вырезать идеально квадратное отверстие становится невозможным.
В итоге, если конструкция как у нас опирается на перпендикулярное удержание деталей в пазах – в чертеже нужно закладывать что любой внутренний угол будет с радиусом 0.6 мм.
На самом деле, все эти нюансы я пытался выпытать у контор-резчиков, но в 100% случаев они на подобные вопросы не отвечают из-за загруженности – о чём вкратце в следующем параграфе.
Поиск компании и заказ
На самом деле, технология лаз. резки металла доступна с далёких 70-х годов, сразу как была отработана конструкция мощных газовых CO2 лазеров… Однако доступность этой технологии для небольших производств, и даже отдельных людей у нас начала подходить только сейчас.О трудностях заказа лазерных металлов:
На 2019-й год в Киеве можно найти около 40-ка объявлений об услуге лаз. резки, начиная с предложений от крупных компаний которые могут резать метровые стальные плиты до 20 мм толщиной, и заканчивая слабыми домашними станками с полем 300x300 мм.
Так вот, даже при наличии 40-ка таких точек только в столице – загруженность у них просто колоссальная, что делает невозможным обращение только к одной или двум конторам с понравившимся объявлением.
Лично я пробовал заказывать 3 раза в течении года. В случае первых двух обращался лишь к 3-4 конторам за раз, без готового к производству чертежа, и попутно задавая вопросы относительно производства.
На первые 2 попытки я получил около 0 ответов на E-mail, а в случае звонка по телефону те обещали что мне перезвонит производственный отдел – чего естественно не случалось. :)
На 3-й раз уже решил брать «быка за рога» – был нарисован готовый чертёж, который я имел полные намерения заказать в количестве >1 штук, не было задано никаких дополнительных вопросов(просто сделайте, это), и письмо было разослано сразу в 12 местных контор за раз.
Примерно, только в течении 4-х дней мне ответили аж 3 конторы. :)
Я начал одинаково общаться со всеми тремя, в процессе чего 2 быстро заглохли, оставив лишь одну.
С последней так же, разговор получался весьма неконструктивный – я сразу требовал назвать сумму и счёт куда её можно оплатить, дабы заказ уже точно ушел в работу, но с другой стороны лилась откровенная вода со скоростью 2-3 ответа в день. Вплоть до того что ушло 10 сообщений и 3 дня перед тем как я получил возможность сбросить им предоплату.
Для примера, лично я стараюсь уже в первом ответе на заказ дать человеку всё необходимое дабы тот мог произвести оплату. :)
Да, в производстве заказ находился ещё целых 2 недели, при которых я 4 раза спрашивал как там дела.
Это при том что с CNC-станком вырезать три коробочки это буквально работа 5-ти минут.
Так вот, даже при наличии 40-ка таких точек только в столице – загруженность у них просто колоссальная, что делает невозможным обращение только к одной или двум конторам с понравившимся объявлением.
Лично я пробовал заказывать 3 раза в течении года. В случае первых двух обращался лишь к 3-4 конторам за раз, без готового к производству чертежа, и попутно задавая вопросы относительно производства.
На первые 2 попытки я получил около 0 ответов на E-mail, а в случае звонка по телефону те обещали что мне перезвонит производственный отдел – чего естественно не случалось. :)
На 3-й раз уже решил брать «быка за рога» – был нарисован готовый чертёж, который я имел полные намерения заказать в количестве >1 штук, не было задано никаких дополнительных вопросов(просто сделайте, это), и письмо было разослано сразу в 12 местных контор за раз.
Примерно, только в течении 4-х дней мне ответили аж 3 конторы. :)
Я начал одинаково общаться со всеми тремя, в процессе чего 2 быстро заглохли, оставив лишь одну.
С последней так же, разговор получался весьма неконструктивный – я сразу требовал назвать сумму и счёт куда её можно оплатить, дабы заказ уже точно ушел в работу, но с другой стороны лилась откровенная вода со скоростью 2-3 ответа в день. Вплоть до того что ушло 10 сообщений и 3 дня перед тем как я получил возможность сбросить им предоплату.
Для примера, лично я стараюсь уже в первом ответе на заказ дать человеку всё необходимое дабы тот мог произвести оплату. :)
Да, в производстве заказ находился ещё целых 2 недели, при которых я 4 раза спрашивал как там дела.
Это при том что с CNC-станком вырезать три коробочки это буквально работа 5-ти минут.
Всё вышеперечисленное может показаться ужасным примером, как люди могут не уметь, или не хотеть работать – но как показывает практика, именно так оперируют конторы у которых никогда не бывает дефицита с заказами.
И прибыв на место мы в этом убедились.
Что же получилось в итоге
Я и BSVi заехали в контору на велосипедах – это оказался небольшой, но прилично выглядящий 2-этажный частный домик.Это фотка Google Street View от 2015-го года где пока всё пусто, но в 2019-м там весь двор заложен материалом, кубами готовых заказов, и вокруг бегают люди примерно как по муравейнику. :)
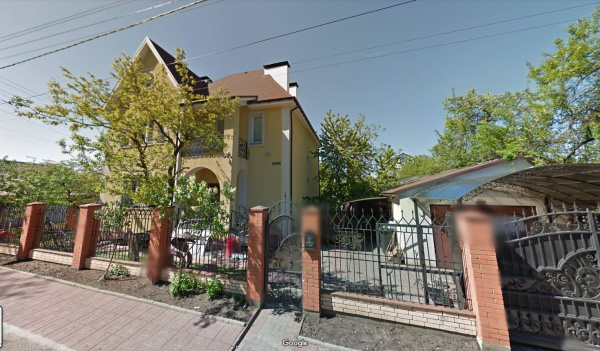
Внутри дом оказался полностью переоборудован под офисы, складские помещения и т.п. – как минимум там постоянно работают человек 20. На втором этаже нам быстро отдали пакет с деталями, и готово.
Но мы ещё задержались, т.к. там было несколько интересных стендов с готовыми образцами.
Там же, из кабинета колл-центра мы краем уха услышали очень крутую цифру – оказалось что ихний лазерный станок загружен примерно на 1000 часов вперёд, или же 41 день.
Вот примерно так обстоят дела, так что получить наши 3 коробочки в течении 2-х недель это ещё было быстро. :)
Кстати, судя по тому что мы видели во дворе – типичными заказами для этой конторы являются 50-200 комплектов за раз, причем не просто вырезанные, а и с элементами CNC-гибки.
Кстати, уже на месте стало ясно, что коробочки по моему чертежу не собираются. :)
Дядька, отдававший детальки сразу пояснил что нужно было учесть радиусы – в принципе справедливо, так что уже дома мне пришлось поработать надфилем дабы чуть сточить крепёжные зубцы стеночек.
Ну, а когда коробки уже собраны – давайте посмотрим что получилось!
Углеродистая сталь
Наверное, эта коробочка выглядит наиболее впечатляюще с эстетической точки зрения – тёмный металл с матовой поверхностью, оттенком немного напоминающим титан. Кромки реза окрасились в тёмно-фиолетовый цвет от оксидации.В общем, действительно красиво:
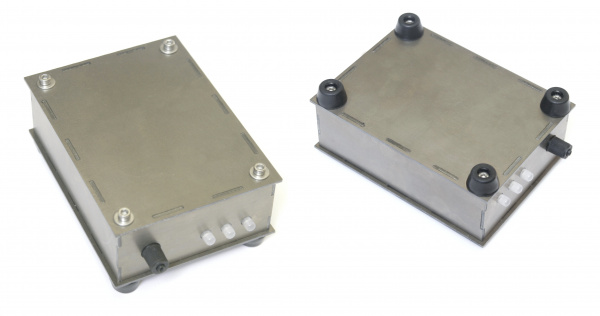
Этот корпус я собрал первым, и в него же пошла платка SD для теста.
Прямо, будто для неё и сделано(гы-гы), жаль что у SD уже есть свой замечательный корпус. :)
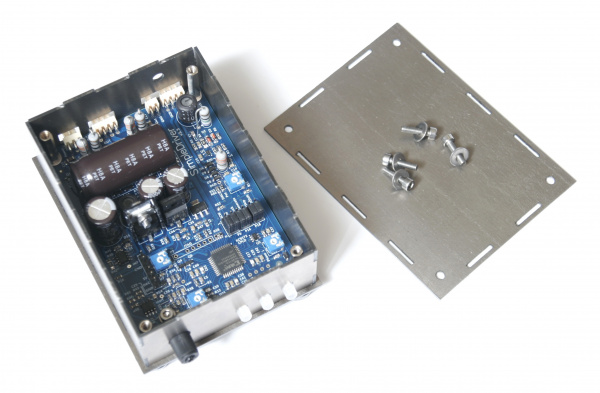
Но красота красотой, всё же не стоит забывать с чем мы имеем дело. Даже при наличии специального оксида, не хранись эта коробочка в музейных условиях – она всего за несколько лет окрасится в коричневый. :)
Даже забирая детальки – они уже были смочены в масле дабы дополнительно предохранить их от коррозии.
По-правильному, для долговечности простую сталь обязательно в начале отдают на пескоструйную обработку, а после покрывают слоем порошка или краски. Для особой долговечности – ещё и слоем лака.
Наиболее распространен такой подход в автомобилях, где кузова традиционно делают из обычной стали для удешевления производства, а потом красят и лакируют – иначе те бы покрывались ржавчиной менее чем за год.
В контраст этому, будь корпус любого авто сделан из нержавейки – он совершенно не нуждался бы в покраске, оставаясь несгниваемым на протяжении многих десятилетий вперёд. :)
Если конечно у вас не идут кислотные дожди, но так ведь – и золото растворяется в царской водке.
Нержавеющая сталь
Она оказалась значительно прочнее предыдущего экземпляра, и у меня ушло где-то 6 часов только чтобы подточить кончики надфилем и собрать этот корпус. Каждая вставленная стеночка была небольшой победой. :DКромка получилась немного острая, и всё время казалось что об детали из нержавейки можно порезаться – благо этого не случилось. Обращаясь с этими детальками есть чувство как будто это осколки кухонного ножа – очень твёрдые, прочные, и звенят как монеты.
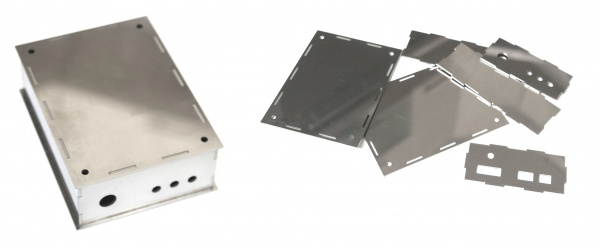
Выглядит корпус по-своему привлекательно, как будто сделан из зеркала т.к. использовался шлифованный лист.
Плюсы у этого материала достаточно значительные – нержавейка очень инертный материал, устройство в таком корпусе буквально можно закопать в землю на 100+ лет, и достать его абсолютно таким же блестящим.
Прочности так же не отбавляй, такой корпус можно бросать об стену, по нему можно проехаться КАМАЗом и тот наверняка выдержит.
Что есть хорошо!
Но что же касательно недостатков?
Я почти сразу заметил что нержавейка царапает сама себя – причем абсолютное большинство царапин возникает ещё при хранении т.к. листы трутся друг об друга. Царапины не особо бросаются в глаза, но на будущее всё же есть смысл найти матовые листы.
Ну и ещё заметка – сплавы нерж. стали бывают очень разные, отличающиеся как по твёрдости, так и по магнитным свойствам. Коробочка, которую вырезали мне оказалась из магнитной стали, что не лучший вариант для работы в мощных электромагнитных полях. Для наших применений нужно обязательно обращать внимание на марку сплава.
Я точно знаю что не магнитится марка AISI 304(она же 08Х18Н10) – но подобных существуют десятки.
Нюансы есть, но в целом – по мне корпуса из нержавейки это пока самый привлекательный вариант, в частности т.к. они не потребуют последующей обработки и могут собираться из деталек «как есть». Нержавейка так же позволит нанести на неё практически вечную гравировку лазером, в отличии от нанесения надписей краской, или вообще наклейками которые слезут уже в первый год.
Local P.S. У меня есть некая тяга к вечным вещам. :)
Алюминий
Вот здесь конечно получился фейл, при том что алюминиевый корпус я ожидал использовать как основной.Конечно, можно предположить что детали просто вырезали из гнилого листа с затонувшей подлодки, но судя по тому что торцы тоже имеют оксидацию – поверхность деталей наверняка была покоцана именно в процессе реза.
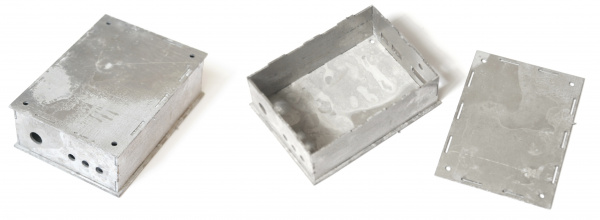
Ну, начнём с того, что опробованная контора оказалось в принципе не режет алюминий лазером – для этого нужны специально заточенные станки, решающие проблему высокой отражаемости IR-диапазона алюминием обратно в оптику, что может разрушить лазер. Даже по мощности, прорезать 1.5 мм алюминий это примерно как резать 10 мм углеродистую сталь. :)
Уже забирая детальки нам сказали что вместо лазера эта коробочка была вырезана другой технологией – «гидроабразивной резкой», более известной как waterjet cutting.
Процесс вообще тоже прикольный, в нём используется струя воды под высоким давлением, в которую подмешаны микроскопические гранулы абразива: en.wikipedia.org/wiki/Water_jet_cutter
Им можно резать такие экзотические материалы как стекло, камень, твёрдую резину, ну и алюминий вплоть до 4+ см толщиной.
Опробовать конечно было интересно, но всё же результат по мне вышел не очень – абразив сильно исцарапал поверхность, и качественно отшлифовать детали такой коробочки займёт часа 2 используя орбитальную шлифмашинку.
Для хоть сколько-нибудь серийного производства это не годится.
В добавок, на каждой алюминиевой детальке есть по вот такому, чуток закрученному усику:
Резка waterjet'ом проходит над ёмкостью с водой, и очевидно – товарищу за станком было влом мочить руку по локоть дабы доставать детали – он выставил галку «не дорезать», а потом открутил детальки с алюминиевого листа.
Если здесь так – думаю с оксидацией тоже как-то нарушили технологию – например деталь лежала мокрой, и у неё не мог образоваться защитный оксидный слой. Так то, в сети полно фотографий ватерджет-резки где на выходе абсолютно чистые алюминиевые детальки.
В общем, с алюминием ещё буду пробовать – причем желательно найти именно лазерную резку, ибо струя ватерджета достаточно не малая – судя по радиусам на внутренних углах она уже достигает где-то между 1 и 1.5 мм.
Заключения
Ну, думаю эксперимент можно считать более чем стоящим, а технологию освоенной.О нюансах мы уже знаем, так что следующими на очереди будут рабочие корпуса для гитар-интерчика. :)
При следующем заказе я обязательно поинтересуюсь что же случилось с алюминием, резать буду из матовой немагнитной нержавейки с учётом внутренних углов, ну и чисто ради теста надо ещё опробовать гибочку, может когда пригодится.
Как обычно, если у вас есть вопросы или замечания – их можно оставить в комментариях снизу, или же написать мне на почту: eugene.negrobov@gmail.com
Кто дочитал простыню – молодец. :)
13 комментариев
Проблема:
Её решение. :D
Можно спросить у Сергея или у Боди, но пока попробую так ответить.
Источников наводки обычно 3 штуки:
1. Прямая ловля сетевых 50 Гц, из проводки в стенах.
Лечится полным экранированием всего тракта – начиная с внутренностей гитары(её обклеивают металл. скотчем), дальше идя по экранированному кабелю, и заканчивая нутрощами усилка(если он самодельный);
2. Отсутствие заземления.
Как и в тех же Теслах – экран должен не просто быть, но и ещё в идеале быть подключенным к земле розетки, или хотя бы на штырь воткнутый на 2 метра в землю и облитый водой.
Проверить есть ли контакт с землёй по всему тракту можно прозвонив continuity мультметром между 3-м контактом на вилке усилка и всеми экранами. Естественно, розетка тоже должна быть земляной. :)
3. Если что-то в системе запитано от 50 Гц железного трансформатора, то эта зараза может где-то пролазить и вызывать осцилляции. Нужно имплементить такую штуку на платках как star ground.
Один раз я так заводской усилок починил кстати, отпаял провод с разъёма питания и подпаял напрямую к электролиту на платке – ранее не дававший спать гул усилка пропал.
На дорогих аудиокабелях по крайней мере 3-го контакта нету:
Может провод какой-то дешманский и он без эрана, ну или экран порвался. :)
Точно так же, как с листа обдираются все стикеры, иначе дофигакиловаттная дура в этом месте металл не прорежет.
Очень сомневаюсь. Углеродистая сталь это не «то, что ржавеет», а то, что имеет определенный уровень углерода. Углеродистые стали это те, из которых делают ножи, напильники, резцы. А листовой прокат больше похож на то, из чего делают гвозди. Есть конечно и 65Х в листах, но сомневаюсь, что вы из нее заказывали. Кромки бы подкалились так, что она сточила бы твой надфиль. У тебя это с нержой произошло, похоже. А так обычно нержа не лучший материал по мех. характеристикам, будь то твердость и износостойкость. Поэтому хорошие лезвия ножей как правило из «ржавейки». Но вообще конечно сплавов дофига, есть и всякие едреные нержи, но они и очень недешевы. То, что твоя нержавейка магнитится говорит как раз о том, что это переходный вариант между нержавейкой и чернухой. Вполне возможно в условиях влажности даже будет темнеть… При этом по мех свойствам она будет лучше тех, что не магнитятся — те вязкие и менее прочные.
Zanuda mode OFF…
Так то, любая железка вокруг нас – углеродистая сталь, ибо очистить железо до состояния 99.99% крайне сложно и дорого.
Реактивное железо для лабораторий буквально стоит в районе $150 за 100 грамм.
Тут такое, уже придирки – инструментальную сталь вообще вроде называют «высокоуглеродистой»… Причем это тоже сбивает с толку, т.к. процентная составляющая углерода там не больше 2%. Где больше – это уже не сталь, а чугун. :)
Про масло для лучшей резки не знал – думал там спецово кто-то из баллончика силиконовой смазкой пшикает.
Насчет нержавейки – я честно не представляю из чего мне мне те детальки вырезали.
Уже убедился что она не такая и твёрдая как изначально казалось – что логично, иначе она бы не царапалась.
Кромка похоже действительно получилась твёрдая именно из-за лазера. Интересно что следов реза не осталось, никаких потемнений, цветов побежалости и т.д.
Вообще у меня дома есть 1.5 мм лист немагнитной нержавейки, как раз крутой.
Не магнитится, не гнётся, и не царапается – видимо холоднокатанная. Когда-то купил на барахолке у металлиста, надо узнать что там за сплав. Пока я из него кухонный ножик сделал, юзаю в кулинарном деле. :)
Да, насчет магнитности – как-то гуглил эту тему, и таки там оно более хитро.
Нержавейки бывают как магнитные, так и немагнитные – зависит от состава сплава. Немагнитных значительно меньше, и получается так только при каких-то очень особых концентрациях хрома/никеля или хрома/молибдена. Т.е. магнитность это не показатель что «нержавейка больше ржавейка чем нержавейка». :)
Ржавеет ли та нержа которая у меня – по идее можно проверить химически. Это уже отдельный параметр для сплавов.
Но то что бывают абсолютно несгнивающие нержавейки знаю из личного опыта – при копе с миноискателем можно найти в земле кусочки нержавейки, пролежвашие там с WWII и до сих пор сохранившие блеск. :)
Как-то ездил с одними дядьками копать под Киевом, там видел огрызок нацистской пулемётной ленты от MG-42 из нержи.
P.S. Кстати, я отшлифовал корпуса из нержи и алюминия, надо как-то зафотать. Матовые значительно красивей.
Была идея делать из жесткого пластика с залитой внутрь арматурой-каркасом, но как-то не пошло…
А кузова для автомобилей из нержавейки делали с самой ранней истории автомобилестроения, но из-за её дороговизны касалось это в основном авто премиум-класса. Кстати, многие такие авто 20-х и 30-х годов дошли до нас именно из-за несгниваемости:
Сегодня нержавейка значительно подешевела, и стоит в среднем всего в 3-5 раз дороже чем чёрный металл.
Как-то пытался гуглить почему по прежнему те же авто не делают из нержавейки, и ответ в основном сводился к следующему:
Типичная жизнь современного авто составляет 5-10 лет, этого мало чтобы проржавел кузов, но уже достаточно дабы расшаталось/порепалось/отпало в автомобиле вообще всё, и из-за низкой ремонтопригодности его оставалось только выбросить на помойку. Т.е. сейчас всё равно в принципе никто не делает карбюраторных пикапов как в американскиз фильмах 70-х, которые можно водить 30 лет подряд и ремонтировать в чистом поле. :)
Но часто количество нужно значительно меньше, например 50 деталек для какой-нибудь прототипной серии(иногда – 5 деталек).
Вот тогда днём и с фонарём человека не сыщешь, который возьмётся делать.
Сейчас лайфхак нашел – мелкое нужно заказывать не в своём городе, а где-то по областям.
Когда в столице контора перегружены, и им заказы сыпятся как с самосвала и те ими перебирают(сейчас намного сильнее, чем в 2019-м) – в областях народ сидит без гроша и заказы им приходят крайне редко. :)
На деле, может занять всего 3 дня от заказа и до получения деталек на Новой Почте, если заказать где-то в ПГТ Кировоградской области… И месяц если заказывать в Киеве у конторы под домом, где можно зайти и забрать пешком.
Такая реалия жизни. :)